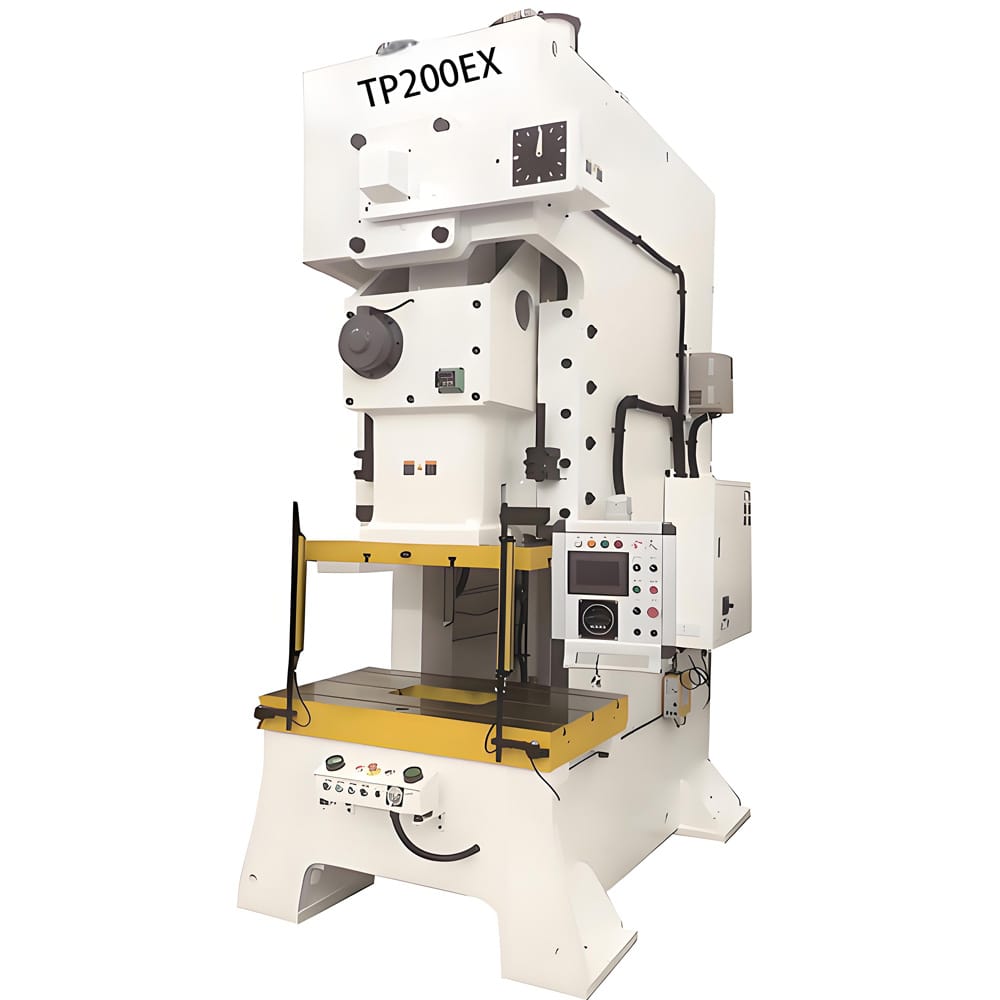
Customize Your TNB-HO Series Electric ServoPress: 45Tons | 66Tons | 88Tons | 150Tons | 220Tons | 330Tons | 440Tons | 550Tons | 660Tons
The TNB-HO Series Gantry High-Speed Servo Press (45-660T) is engineered for precision stamping in automotive, aerospace, and electronics industries. Featuring zero-clearance ultra-long axial bearings, forced lubrication cooling, and a pre-stressed rigid frame, it delivers ±0.01mm repeatability, extends mold lifespan by 30%, and operates at <75dB noise levels. Ideal for high-volume, high-tolerance manufacturing with unmatched cost efficiency.
Frictionless Motion: Sliding block guide posts eliminate clearance, reducing mold wear and downtime.
Ultra-Precision: Dynamic/static accuracy exceeds industry standards (±0.01mm tolerance).
Bolt + High-Pressure Oil Preload: Enhances frame rigidity by 50%, ensuring long-term stability.
High-Strength Cast Body: Stress-relieved design withstands heavy-duty stamping.
Thermal Control: Reduces base heat deformation, improving part consistency by 20%.
Extended Machine Life: Lowers maintenance costs by 15% annually.
High-Response Servo Motor: Adjustable speed (2-800 SPM) for complex dies or rapid production.
Quiet Operation (<75dB): Dynamic balance minimizes vibration, ideal for noise-sensitive facilities.
CE/ISO Certified: Photoelectric guards, emergency stops, and overload protection.
30% Energy Savings: Outperforms hydraulic presses in energy efficiency.
Engine brackets, EV battery housings, structural components.
Titanium fasteners, turbine blade forming.
5G shielding covers, micro-connectors.
Solar panel frames, hydrogen fuel cell plates.
Model | TNB45HO | TNB66HO | TNB88HO | TNB150HO | TNB220HO | TNB330HO | TNB440HO | TNB550HO | TNB660HO |
---|---|---|---|---|---|---|---|---|---|
Nominal Force (kN) |
450 |
660 |
880 |
1500 |
2200 |
3300 |
4400 |
5500 |
6600 |
Capability occurrence point |
1.6 |
2 |
2 |
2 |
2 |
2 |
2 |
2 |
2 |
Slide Stroke (mm) |
30 |
30 |
30 |
30 |
30 |
30 |
30 |
50 |
50 |
Single Strokes Per Minute (SPM) |
2-800 |
2-800 |
2-700 |
2-700 |
2-600 |
2-400 |
2-350 |
2-250 |
2-250 |
Inching Strokes |
handwheel pulse |
handwheel pulse |
handwheel pulse |
handwheel pulse |
handwheel pulse |
handwheel pulse |
handwheel pulse |
handwheel pulse |
handwheel pulse |
Maximum Die Height (mm) |
240-290 |
300-350 |
330-380 |
360-410 |
370-420 |
400-450 |
420-470 |
500-550 |
520-570 |
Die Height Adjustment (mm) |
50 |
50 |
50 |
50 |
50 |
50 |
50 |
50 |
50 |
Dimension of worktable L-R (mm) |
750 |
950 |
1100 |
1400 |
1900 |
2400 |
2800 |
3200 |
3200 |
Dimension of worktable F-B (mm) |
550 |
650 |
750 |
850 |
1000 |
1000 |
1200 |
1400 |
1400 |
Size of slide bottom L-R(mm) |
750 |
950 |
1100 |
1400 |
1900 |
2400 |
2800 |
3200 |
3200 |
Size of slide bottom F-B(mm) |
380 |
420 |
500 |
600 |
750 |
900 |
1100 |
1200 |
1200 |
Slide Adjustment Method |
Electric Adjustment |
Electric Adjustment |
Electric Adjustment |
Electric Adjustment |
Electric Adjustment |
Electric Adjustment |
Electric Adjustment |
Electric Adjustment |
Electric Adjustment |
Working table plate blanking hole L-R(mm) |
550 |
700 |
800 |
1000 |
1400 |
2200 |
2200 |
2700 |
2700 |
Working table plate blanking hole F-B(mm) |
125 |
125 |
150 |
200 |
300 |
300 |
400 |
500 |
500 |
Height of feeding line(mm) |
130±50 |
160±50 |
175±50 |
195±50 |
200±50 |
210±50 |
220±50 |
240±50 |
240±50 |
FAQS For the Servo Press Industry
Our gantry-type high-speed precision servo press (TNB-HO Series) features ultra-long axial bearings with zero clearance and preloaded bolt-extended guide rails, achieving dynamic and static precision exceeding super-grade standards, significantly extending mold lifespan. The servo-driven technology enables precise stroke speed control (2-800 spm), lower energy consumption, and a forced lubrication cooling system to ensure long-term stability and reduced consumable costs. Traditional presses lag behind in precision, energy efficiency, and maintenance costs.
The fuselage uses high-strength castings treated with internal stress elimination, combined with bolt-fastened frame structures preloaded with high-pressure oil to enhance rigidity. The guide posts employ zero-clearance ultra-long axial bearings, while preloaded bolts on extended guide rails ensure stable dynamic/static precision. The forced lubrication cooling system minimizes thermal deformation, further safeguarding accuracy.
Designed for low consumables, our presses reduce wear via a forced lubrication system and circulating cooling. Critical components like high-alloy steel crankshafts and saw-tooth sets undergo heat treatment and precision grinding for extended durability. Standard configurations include a lubricant circulation cooling system and an electric mold height adjuster (0.01mm precision), ensuring easy maintenance and lower lifetime costs than traditional presses.
Yes! Our high-speed servo presses are compatible with optional devices like high-speed feeders, straighteners, and quick clamping systems (e.g., double-head feeding racks, hydraulic mold lifters). The high-sensitivity servo drive ensures precise positioning, enabling seamless automation for industries like automotive, electronics, and appliances requiring high-precision stamping.
Safety features include an oil-pressure sliding block lock, front/rear safety doors, and fail-safe servo drives. Environmentally, the forced lubrication system minimizes oil waste, while dynamic balance design reduces noise/vibration, complying with international eco-standards.
The standard electric mold height adjuster offers 0.01mm display precision, supports 30 mold data presets, and batch control. All models (TNB45HQ to TNB660HQ) provide 50mm mold height adjustment, paired with a reversible handwheel for flexible, pinpoint accuracy.
Feeding line heights range from 130mm to 240mm (±50mm), with maximum capacities up to 6600kN, suitable for high-strength alloys, copper, and aluminum. Worktable sizes span 750mm×550mm to 3200mm×1400mm, accommodating diverse stamping needs.
Absolutely! Beyond standard features (e.g., split control box, work lights), optional add-ons include a lower dead point detector, hydraulic shockproof feet, and quick mold-change systems. Technical specs (stroke, table size) can be tailored to meet unique production requirements.
We offer global technical support, installation guidance, and scheduled maintenance. Critical components (e.g., servo drives, high-alloy steel parts) come with extended warranties for worry-free operation.
Specializing in precision servo presses and efficient pneumatic presses, we deliver advanced stamping solutions for global manufacturing excellence.
@ 2025 FT Servo Press. All right reserved.
Fill out the form below, and we will be in touch shortly.