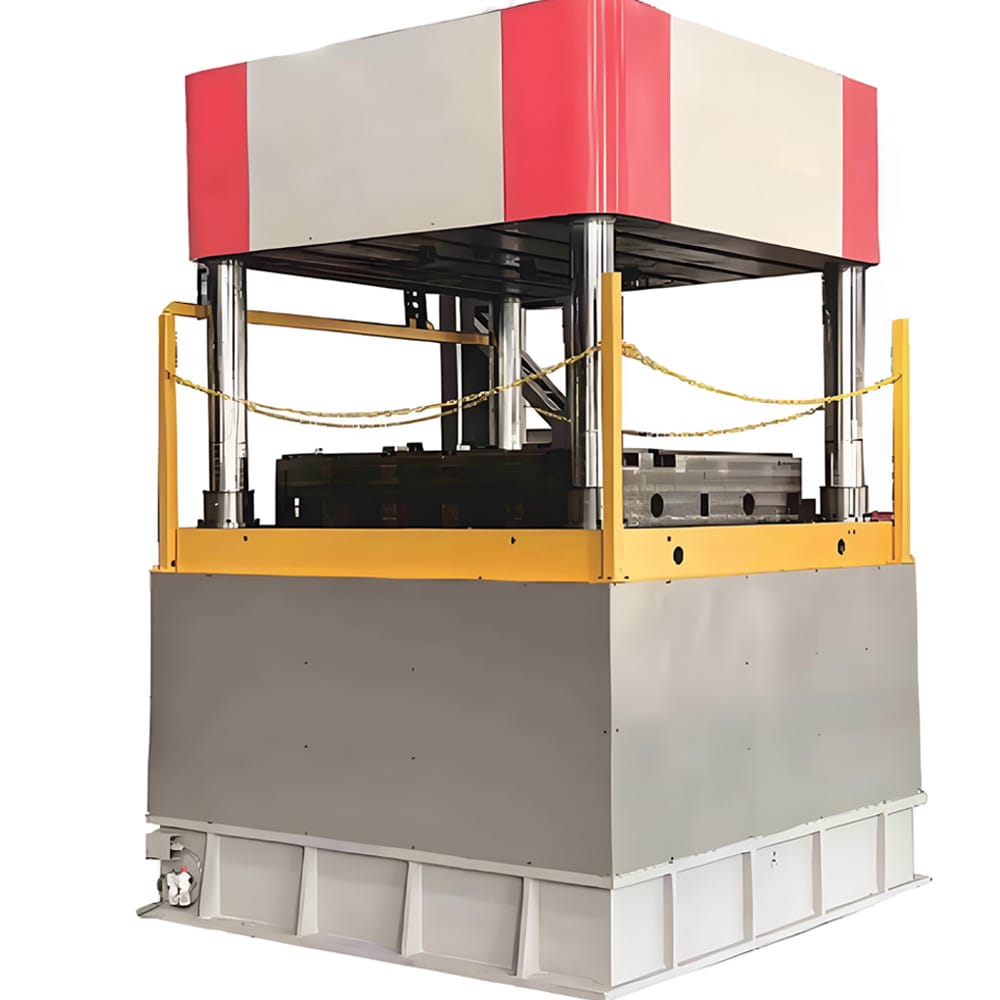
We’ll take you through the key factors—from tonnage to energy efficiency—to help you make an informed decision. Let’s dive in!
Tonnage measures the maximum force a servo press can exert, it is critical for tasks like stamping, bending, or deep drawing.
Material & Thickness: Harder materials (e.g., steel) or thicker sheets demand higher tonnage. For example, punching a 10mm steel plate may require 100-150 tons.
Force Calculations: Use material-specific tonnage charts or engineering formulas. Always add a 20-30% safety margin to avoid overloading.
Servo Advantage: Unlike traditional presses, servo models offer dynamic force control, adjusting tonnage mid-stroke for precision.
Servo presses shine in industries requiring accuracy and flexibility. Popular uses include:
Precision Forming: Electronics, automotive, and aerospace parts (e.g., battery housings, connectors).
High-Speed Stamping: Ideal for metal components like brackets or panels.
Deep Drawing: Complex shapes such as automotive body parts or cookware.
Assembly Tasks: Press-fitting bearings or fasteners with controlled force.
±0.01mm accuracy for tight tolerances.
Programmable motion profiles handle multiple tasks in one cycle.
Energy savings of up to 50% compared to hydraulic presses.
Stroke Length: Ensure the ram travel suits your application. Deep drawing needs 200-300mm strokes; stamping may require 50-100mm.
Speed Control: Adjust speeds for high-volume stamping (fast) or delicate forming (slow).
Cycle Time Optimization: Servo presses reduce idle time with customizable motion profiles, boosting output.
Bed Dimensions: Confirm the press accommodates your largest die or workpiece. Measure tooling and add clearance.
Shut Height: Match the closed ram-to-bed distance to your die height.
Modular Options: Look for T-slots or customizable beds for flexible setups.
User-Friendly Interface: Intuitive HMIs simplify programming force, speed, and position.
Real-Time Data Monitoring: Track force, displacement, and quality metrics for Industry 4.0 integration.
Recipe Storage: Save settings for quick changeovers in mixed production runs.
Lower Power Use: Servo motors consume energy only during motion, slashing costs by 20-50%.
Reduced Maintenance: Fewer mechanical parts (no flywheels/clutches) mean less downtime.
Quieter Operation: Improved workplace safety and comfort.
Upfront Cost vs. Savings: Higher initial investment pays off through energy efficiency, reduced scrap, and versatility.
ROI Boosters:
Fewer defects due to precision.
One press handles multiple jobs, cutting equipment costs.
Faster setups minimize downtime.
Supplier Support: Prioritize brands offering training, spare parts, and reliable service.
Factory Footprint: Compact designs save floor space.
Safety Features: Ensure overload protection, emergency stops, and light curtains.
Future-Proofing: Opt for scalability to handle new materials or larger parts.
Automation Integration: Check compatibility with robots or conveyors for smart production lines.
Consult Experts: Share specs (material, part size, volume) with suppliers for tailored advice.
Request Demos: Test the press with your dies to verify performance.
Choosing the right servo press balances tonnage, application needs, and smart features to maximize ROI. Whether you’re stamping lightweight alloys or forming precision aerospace components, this guide ensures you invest wisely. Need personalized advice? Share your project details for tailored recommendations!
👉 [Click here for a free consultation] with an engineer!
Fill out the form below, and we will be in touch shortly.