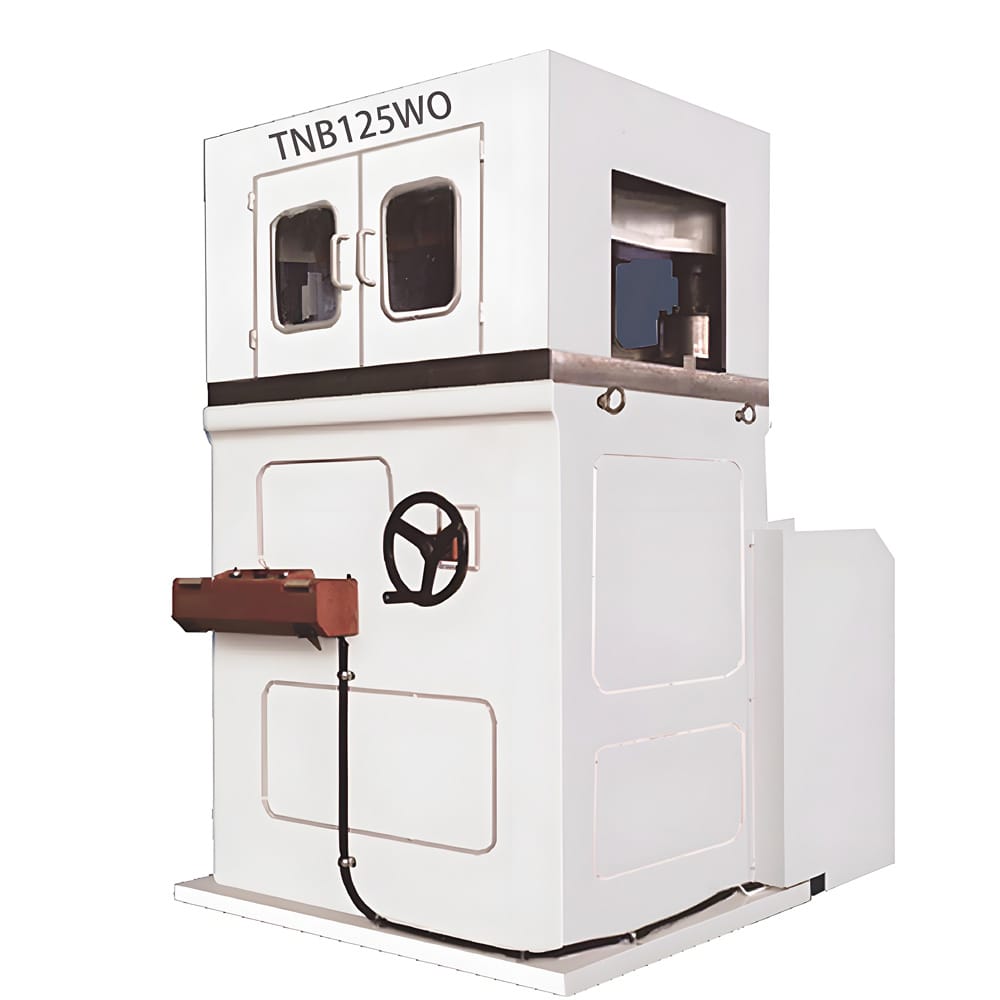
Standard Configuration
- Hydraulic overload protection device
- Manual slide adjustment (≤TP60)
- Motorized slide adjustment (≥TP80)
- Mechanical die height indicator (≤TP60)
- Digital die height indicator (≥TP80)
- Slide and die balance device
- Rotary encoder
- Crankshaft angle indicator
- Air source connection
- Touch screen (pre-break/pre-load/total counter)
- Dry-type combination clutch brake
- Balance cylinder manual lubrication
- Variable frequency drive (VFD)
- Power outlet
- Cycle counter
- Air blow-off device
- Misfeed detection interface
- Double-stroke prevention device
- Maintenance tools and toolbox
- Operation manual
- Electric grease lubrication system
- Vibration isolation feet
- Die lighting system
- Twin solenoid valve
- Main motor reverse operation
- Light curtain safety device
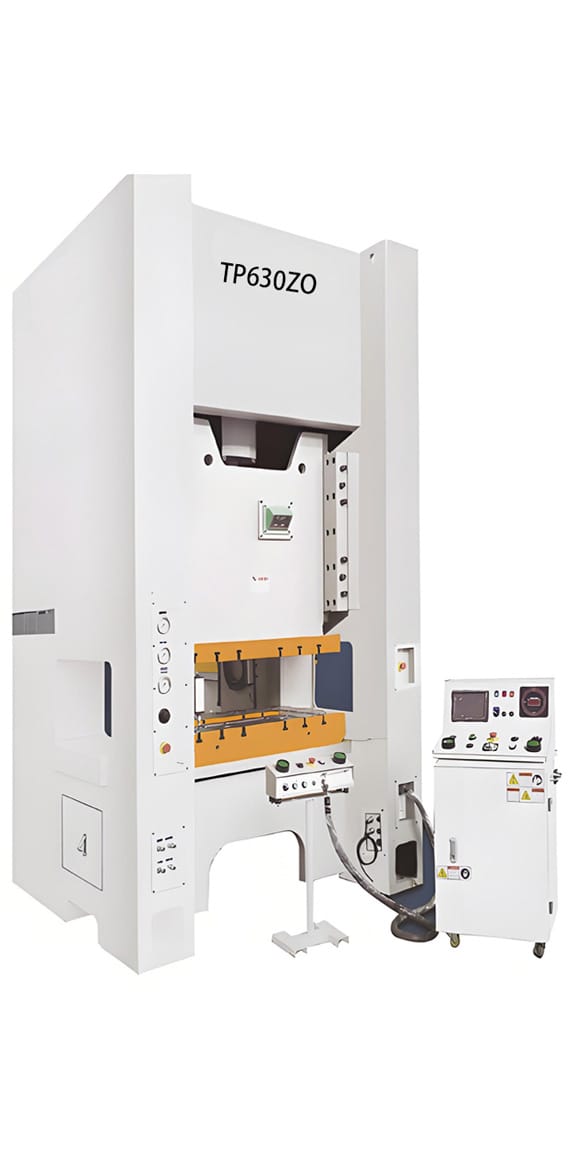
Optional Configurations
- Wet clutch system
- Pneumatic cushion system
- Foot pedal switch
- Upper knock-out device
- "T"-type control panel
- Quick die change system (die lifters/clamps/transfer units)
- Feeders (pneumatic/mechanical/NC types)
- Straightener/leveler
- Robot manipulator
- Coil cradle