Precision Pneumatic Stamping Press
Pneumatic punches press of different models and tonnages for you to choose
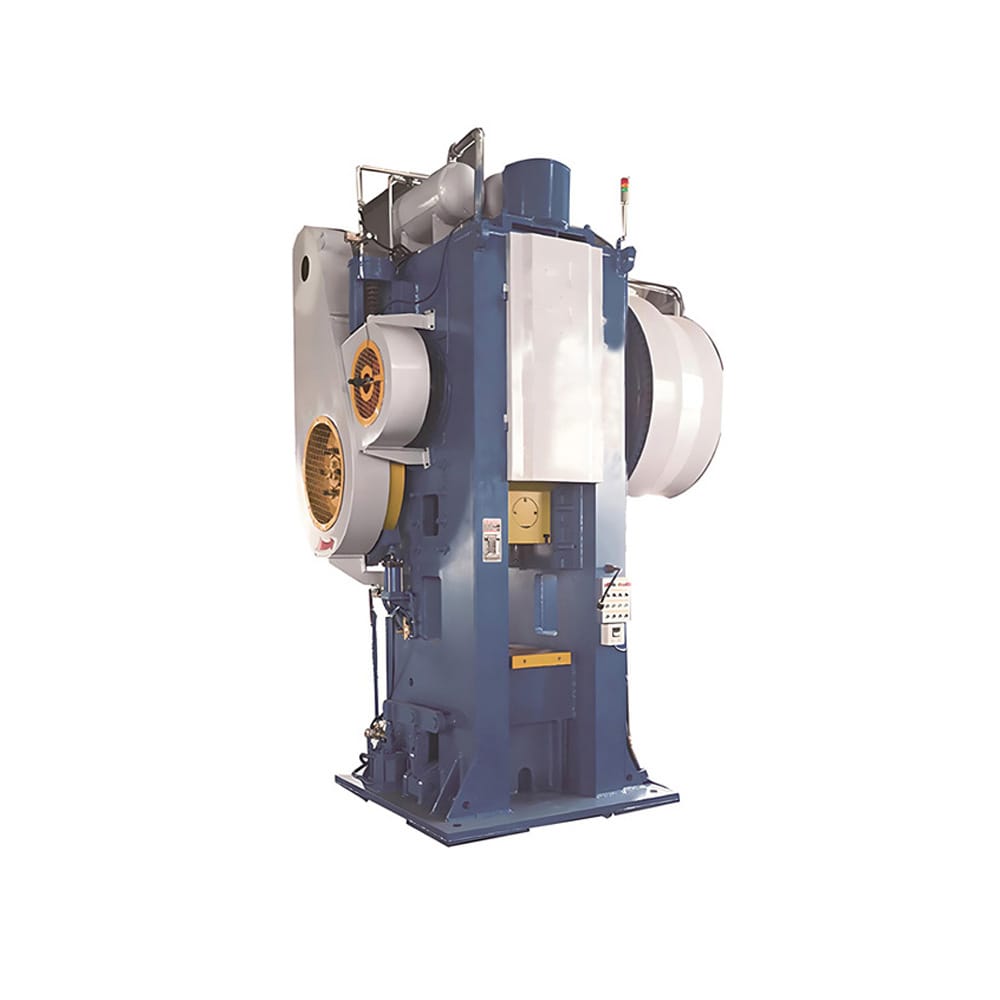
Pneumatic punches press of different models and tonnages for you to choose
Monitors the press load in real-time via a hydraulic system. Automatically cuts off power and halts operation when pressure exceeds safe thresholds, preventing damage to molds and mechanical structures caused by overloads, thereby extending equipment lifespan.
Manual (for TP60 and below): Adjusts slide height manually via a crank or screw, suitable for small presses (TP60 and below), offering simplicity and low maintenance costs.
Electric (for TP60 and above): Uses servo motors for precise slide positioning via touchscreen or control panel, enhancing efficiency and accuracy for large presses (TP60 and above).
Mechanical (for TP60 and below): Displays die height via a mechanical dial or pointer, intuitive but less precise, ideal for low-precision applications.
Digital (for TP60 and above): Integrates a digital display or touchscreen to show millimeter-level die height data, supporting fine-tuning for high-precision stamping.
Balances the weight of the slide and die using pneumatic or hydraulic systems, reducing vibrations during operation to ensure stable stamping and product consistency.
Monitors crankshaft angles and slide positions in real-time, converting mechanical motion into electrical signals for the control system to ensure synchronized and repeatable stamping actions.
Displays crankshaft rotation angles (e.g., 0°–360°), helping operators monitor stamping cycle phases (e.g., top/bottom dead center) and optimize production rhythm.
Connects to an external air source to supply compressed air for pneumatic components (e.g., balance cylinders, air ejectors), ensuring stable automation.
Integrates preset parameters (e.g., pre-cut, preset), production counters, and fault diagnostics to streamline operations and enhance human-machine interaction.
Uses an oil-free design with electromagnetic controls for rapid clutch engagement and braking. Ideal for high-speed continuous stamping with low maintenance.
Provides manual grease injection points for balance cylinders to reduce friction and extend component lifespan.
Standardized industrial power interface for the main motor, control system, and auxiliary devices, ensuring stable operation.
Records and displays stamping cycles for production statistics, efficiency analysis, and maintenance scheduling.
Uses compressed air to automatically clear scraps or finished parts from molds, reducing manual intervention and improving continuous operation efficiency.
Detects material misalignment or jams via photoelectric sensors, triggering automatic shutdowns to prevent mold damage.
Provides mechanical or electrical redundancy (e.g., emergency stop buttons) if primary photoelectric protection fails, ensuring operator safety.
Includes wrenches, grease guns, and specialized tools for daily upkeep and quick repairs, minimizing downtime.
Offers detailed guidelines for installation, operation, and troubleshooting to ensure compliance and maximize performance.
Automatically dispenses grease to critical components (e.g., rails, bearings) at scheduled intervals, reducing wear and extending lifespan.
Absorbs operational vibrations via rubber or hydraulic dampers, reducing noise and protecting floors and nearby equipment.
Built-in LED strips illuminate the mold area for quality checks and mold inspections, reducing human error.
Controls pneumatic components via dual-channel valves, improving response speed and reliability for complex automation.
Allows main motor reversal to clear jams or reset abnormal states, enhancing fault tolerance.
Uses infrared light curtains to cover hazardous zones, stopping the press immediately upon intrusion, compliant with ISO 13849 standards.
Adjusts motor input frequency for stepless speed control, adapting to diverse materials and processes while reducing energy consumption.
Utilizes oil-cooled friction plates to deliver high torque and superior heat dissipation, ideal for heavy-duty stamping operations (e.g., automotive parts) requiring prolonged continuous use.
Adjusts blank holder pressure during deep drawing or forming processes to prevent material wrinkles and ensure uniform part quality.
Allows hands-free operation for manual control of press cycles, enhancing safety and flexibility in small-batch production.
Mechanically or pneumatically ejects stuck parts from the die cavity to minimize downtime and prevent damage.
Ergonomic control panel with centralized buttons and touchscreen for intuitive operation and real-time monitoring of press parameters.
Enables rapid die replacement using integrated tools (die lifter, clamp, die mover), reducing setup time for multi-product manufacturing.
Air Feeder: Uses compressed air to advance materials.
Mechanical Feeder: Driven by press crankshaft for synchronized feeding.
NC Feeder: Programmable servo-driven feeding for high precision.
Flattens coiled metal sheets by removing internal stress, ensuring material flatness before stamping for consistent product quality.
Automates part handling (loading/unloading) to integrate with press cycles, enabling unmanned production lines and reducing labor costs.
Holds and unwinds coiled materials (e.g., steel, aluminum) for continuous feeding into the press line.
If there is no pneumatic punch press that meets your requirements, please contact us.
Fill out the form below, and we will be in touch shortly.