Applications of Servo Presses
Ideal for demanding industries like automotive, aerospace, and electronics manufacturing, servo-electric presses deliver exceptional accuracy for complex stamping, forming, and assembly processes.
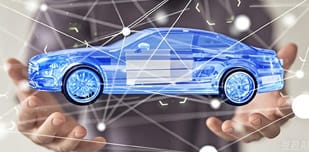
Automotive Manufacturing
- High-speed stamping of body panels, brackets, and EV battery components.
- Multi-stage forming of transmission gears and sensor housings.
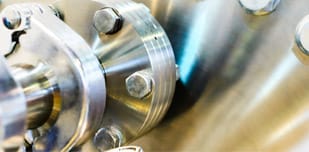
Electronics Manufacturing
- Micro-stamping of connectors, heat sinks, and lead frames.
- Delicate embossing of flexible PCBs and RFID tags.
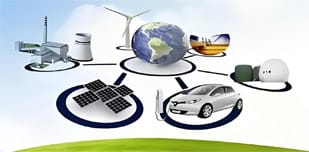
Emerging Applications
- Consumer Tech: Smartphone chassis forming, wearables.
- Energy: Solar cell tab welding, fuel cell bipolar plates.
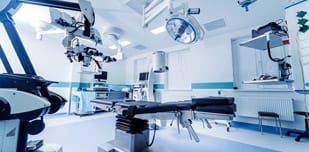
Medical Device Production
- Cleanroom-compatible stamping of surgical tools and implant casings.
- Micro-hole punching in biodegradable stents.