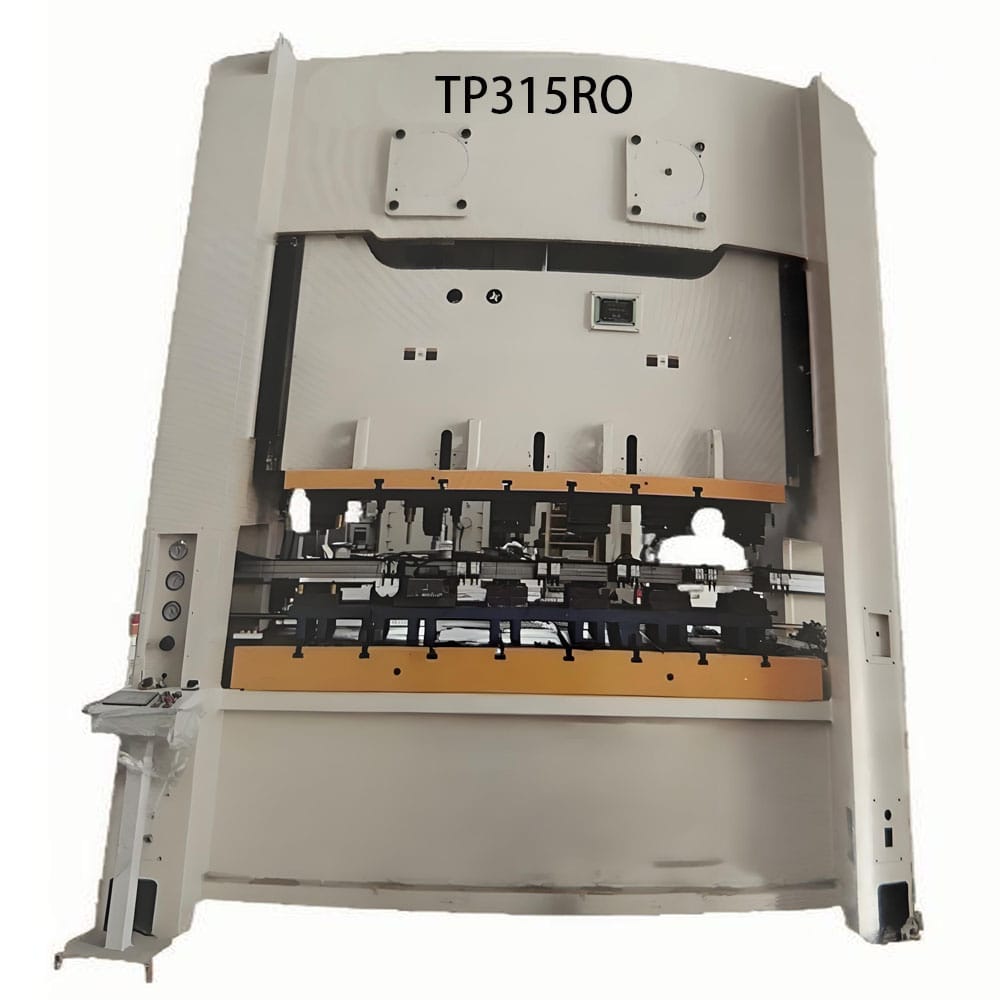
Four-Point Elbow-Type Pull Precision Stamping Solutions Customize Your Electric ServoPress:
5Tons | 15Tons | 25Tons | 35Tons | 45Tons | 65Tons | 110Tons | 125Tons | 150Tons| 200Tons | 250Tons | 300Tons | 400Tons | 500Tons
Clean Production: No oil contamination on the upper workspace. Eliminates post-stamping cleaning and electroplating for non-ferrous metals (e.g., copper, aluminum), enabling direct assembly of stamped terminals and lead frames. Reduces scrap rates and disposal costs.
Lower Drive Advantage: Ensures contamination-free stamping for sensitive materials.
Precision Forming: Minimal lower dead center displacement (±0.01mm tolerance) ensures stable forming quality, perfect for high-precision electronic components.
Anti-Deflection Design: Four-corner synchronized slider movement distributes force evenly, minimizing deformation (<0.02mm) even with complex molds.
Servo Motor Drive: Reduces energy consumption by 30% and increases response speed by 40%. Supports continuous high-speed operation (2-1050 SPM).
Space-Saving: Compact and low-height design (5-500 tons) optimizes floor space and integrates seamlessly with automated production lines.
Multi-Layer Safety: Photoelectric guards, emergency stops, and overload protection comply with CE/ISO standards.
Eco-Friendly: Low noise (<75dB) and zero hydraulic oil leakage, meeting global environmental regulations.
Stamping IC lead frames, connectors, micro-motor components.
Lithium battery electrodes, solar panel brackets, hydrogen fuel cell bipolar plates.
Medical devices, optical components, and high-tolerance industrial parts.
TNB-WO Series: 30% Lower Energy Consumption
Traditional Mechanical Press: High Energy Use
TNB-WO Series: ±0.01mm Tolerance
Traditional Mechanical Press: ±0.05mm Tolerance
TNB-WO Series: Oil-Free Design
Traditional Mechanical Press: Hydraulic Oil Leakage Risks
TNB-WO Series:4-Point Sync, <0.02mm Deform
Traditional Mechanical Press: Single-Point Drive, High Deflection
Scale from 5 Tons to 500 Tons with modular frames,automated coil feeders, Custom bolster plates for ISO/DIN/JIS standards.
Model | TNB5WO | TNB15WO | TNB25WO | TNB35WO | TNB45WO | TNB65WO | TNB150WO | TNB300WO | TNB400WO | TNB500WO | |
---|---|---|---|---|---|---|---|---|---|---|---|
Nominal Force (kN) |
50 |
150 |
250 |
350 |
450 |
650 |
1500 |
3000 |
4000 |
5000 | |
Slide Stroke (mm) |
30 |
30 |
30 |
30 |
30 |
30 |
200 |
220 |
250 |
250 | |
Continuous Stroke |
2-1050 |
2-750 |
2-500 |
2-500 |
2-500 |
2-350 |
2-120 |
2-110 |
2-100 |
2-100 | |
Single Strokes Per Minute (SPM) |
unlimited |
unlimited |
unlimited |
unlimited |
unlimited |
unlimited |
unlimited |
unlimited |
unlimited |
unlimited | |
Inching Strokes |
any |
any |
any |
any |
any |
any |
any |
any |
any |
any | |
Maximum Die Height (mm) |
160 |
180 |
200 |
230 |
240 |
360 |
460 |
500 |
600 |
600 | |
Die Height Adjustment (mm) |
2 |
2 |
2 |
2 |
2 |
2 |
40 |
50 |
50 |
50 | |
Upper Table Size (mm) |
640*440 |
660*460 |
680*480 |
700*500 |
750*500 |
750*500 |
1700*600 |
1750*800 |
1800*850 |
1800*900 | |
Lower Table Size (mm) |
640*580 |
660*600 |
680*620 |
700*640 |
750*640 |
750*640 |
1700*600 |
1750*800 |
1800*850 |
1800*900 | |
Slide Adjustment Method |
Manual Adjustment |
Manual Adjustment |
Manual Adjustment |
Manual Adjustment |
Manual Adjustment |
Manual Adjustment |
Electric Adjustment |
Electric Adjustment |
Electric Adjustment |
Electric Adjustment |
Electric Adjustment |
Airframe form |
pull - down type |
pull - down type |
pull - down type |
pull - down type |
pull - down type |
pull - down type |
pull - down type |
pull - down type |
pull - down type |
pull - down type | |
Press Accuracy |
JIS Class 1 |
JIS Class 1 |
JIS Class 1 |
JIS Class 1 |
JIS Class 1 |
JIS Class 1 |
JIS Class 1 |
JIS Class 1 |
JIS Class 1 |
JIS Class 1 |
FAQS For the Servo Press Industry
The TNB-WO series combines a four-point elbow-type pull mechanism and symmetrical toggle link design, ensuring minimal lower dead center displacement and uniform force distribution. It supports JIS Class 1 press accuracy and integrates anti-eccentric load resistance, making it perfect for stamping terminals, lead frames, and thin non-ferrous metals. Additional features like the electric die height adjustment and photoelectric safety system further enhance precision and operational safety.
The Q.D.C. device reduces downtime by enabling rapid mold swaps, ideal for high-mix production. Combined with the automatic feeding system (feeder, coil stand, straightener) and robotic arm integration, it streamlines workflows, boosts efficiency, and minimizes manual intervention.
The servo-driven motor dynamically adjusts speed and torque, slashing energy waste. Features like the stepless speed control system and low consumables design further reduce power consumption. Its compact footprint (5–500 tons) also lowers facility energy demands.
Absolutely. The four-corner push-pull slider ensures even stress distribution across the entire die surface, even under heavy loads. Models up to 5000 kN nominal force (TNB500) and 600 mm maximum die height are engineered for thick materials with ultra-low deformation rates.
The electric die height adjustment allows precise, tool-free calibration (up to 50 mm in larger models). Paired with the digital die height indicator, operators can achieve micron-level accuracy, reducing setup time and ensuring consistent stamping quality.
Standard safety features include photoelectric protection, misfeed detection, and electromagnetic stroke counters. Optional upgrades like the pneumatic blow-off system and robotic arm support fully automated, hazard-free production lines.
The series spans 5–500 tons, with varying specs:
Smaller models (TNB5–TNB65): Compact size (e.g., 640×440 mm upper table), ideal for thin materials and high-speed tasks (up to 1050 SPM).
Larger models (TNB110–TNB500): Higher force (1100–5000 kN) and taller die heights (up to 600 mm), suited for heavy-duty stamping in automotive or energy sectors.
The oil-free upper worktable eliminates contamination, while the lower drive structure reduces wear. Combined with anti-vibration pads and a maintenance tool kit, downtime is minimized, and machine longevity is extended.
Yes! Optional add-ons like the pneumatic die cushion (for deep drawing) or rotary encoder (for motion control) tailor the press to niche needs, such as solar panel components or EV battery parts.
Its servo technology cuts energy use by 30–50% versus pneumatic presses. The oil-free design and reduced scrap rates (via precision stamping) lower waste disposal costs, supporting green manufacturing goals.
Specializing in precision servo presses and efficient pneumatic presses, we deliver advanced stamping solutions for global manufacturing excellence.
@ 2025 FT Servo Press. All right reserved.
Fill out the form below, and we will be in touch shortly.