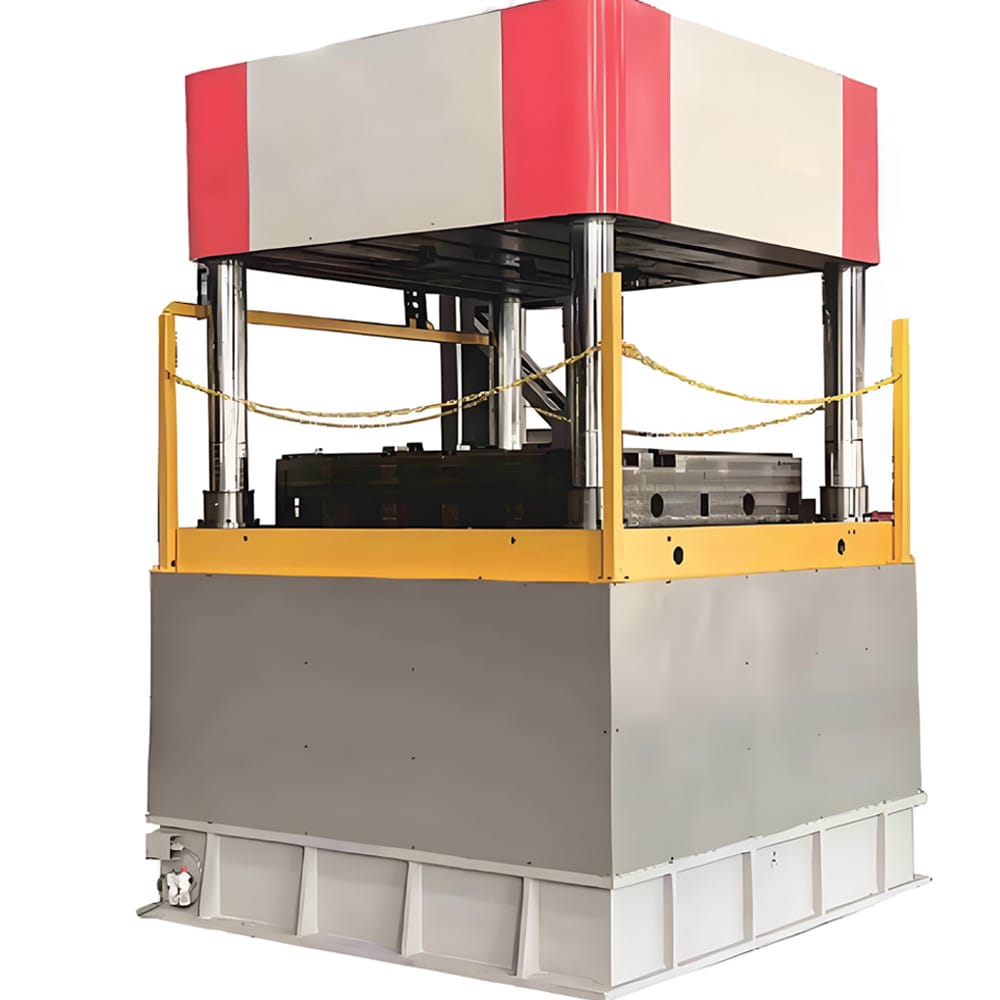
Industrial-Grade Precision Stamping Solutions for Aerospace & Heavy Industries, Customize Your TNC-TD/FD Electric ServoPress: 400Tons | 630Tons | 800Tons | 1000Tons | 1250Tons | 1600Tons | 2000Tons | 2500Tons | 3300Tons| 4000Tons
JIS Grade 1 certification ensures micro-level accuracy for critical components like turbine blades and EV battery casings.
Servo motors activate only during stamping, slashing idle power waste versus traditional presses.
Modular straight-side design minimizes frame deflection (<0.02mm) even at 4,000-ton capacity.
No flywheel, belts, or clutch—maintenance costs reduced by 60%.
Form titanium aircraft brackets with ±0.02mm tolerance.Compatible with superalloys for turbine components.
Produce EV chassis parts with 4,000-ton force and ultra-low noise (<68dB).
Stamp wind turbine flanges and solar panel frames at 70% lower energy cost.
Real-time monitoring of force, speed, and energy use.
70% energy savings align with EU Green Deal targets.
CE, JIS B 6402, ISO 14001 (environmental management).
Laser guards + dual emergency stops.
Scale from 400T to 4,000T with modular frames,automated coil feeders,Custom bolster plates for ISO/DIN/JIS standards.
Model | TNC400 | TNC630 | TNC800 | TNC1000 | TNC1250 | TNC1600 | TNC2000 | TNC2500 | TNC3300 | TNC4000 |
---|---|---|---|---|---|---|---|---|---|---|
Nominal Force (kN) |
4000 |
6300 |
8000 |
10000 |
12500 |
16000 |
20000 |
25000 |
33000 |
40000 |
Slide Stroke (mm) |
400 |
500 |
500 |
500 |
600 |
600 |
600 |
600 |
800 |
1000 |
Continuous Stroke |
2-50 |
2-50 |
2-40 |
2-40 |
2-40 |
2-40 |
2-40 |
2-40 |
2-20 |
2-18 |
Single Strokes Per Minute (SPM) |
unlimited |
unlimited |
unlimited |
unlimited |
unlimited |
unlimited |
unlimited |
unlimited |
unlimited |
unlimited |
Inching Strokes |
any |
any |
any |
any |
any |
any |
any |
any |
any |
any |
Maximum Die Height (mm) |
750 |
1000 |
1000 |
1200 |
1200 |
1200 |
1200 |
1200 |
1200 |
1300 |
Die Height Adjustment (mm) |
300 |
350 |
500 |
500 |
600 |
600 |
600 |
600 |
600 |
600 |
Dimension of worktable L-R (mm) |
3200 |
3600 |
4000 |
4000 |
4500 |
5000 |
5500 |
6000 |
6200 |
6300 |
Dimension of worktable F-B (mm) |
1600 |
1600 |
1800 |
1800 |
1900 |
2000 |
2000 |
2000 |
2600 |
2600 |
Size of slide bottom L-R(mm) |
3200 |
3600 |
4000 |
4000 |
4500 |
5000 |
5500 |
6000 |
6200 |
6300 |
Size of slide bottom F-B(mm) |
1600 |
1600 |
1800 |
1800 |
1900 |
2000 |
2000 |
2000 |
2600 |
2600 |
Electric Adjustment |
Electric Adjustment |
Electric Adjustment |
Electric Adjustment |
Electric Adjustment |
Electric Adjustment |
Electric Adjustment |
Electric Adjustment |
Electric Adjustment |
Electric Adjustment |
Electric Adjustment |
Air Pressure (MPa) |
0.6 |
0.6 |
0.6 |
0.6 |
0.6 |
0.6 |
0.6 |
0.6 |
0.6 |
0.6 |
Press Accuracy |
JIS Class 1 |
JIS Class 1 |
JIS Class 1 |
JIS Class 1 |
JIS Class 1 |
JIS Class 1 |
JIS Class 1 |
JIS Class 1 |
JIS Class 1 |
JIS Class 1 |
Working table moving direction:
Optional: front-side, rear-side, moving out in the front and rear directions, left-side, right-side, moving out in the left and right directions, lateral movement in the left and right directions in T shape, movement in the front and rear directions in T shape.
FAQS For the Servo Press Industry
Our TNC-TD/FD series servo presses feature energy-saving servo motor technology that operates only during stamping, reducing power consumption by 70% compared to ordinary presses. Unlike pneumatic presses, they eliminate flywheels, belts, and clutches, resulting in a maintenance-free, low-noise, and vibration-free design with JIS 1-grade precision.
The servo motor activates only during the pressing cycle, minimizing idle energy waste. Combined with stepless speed regulation and advanced control systems, it ensures optimal energy use while maintaining high productivity.
Standard safety configurations include a photoelectric safety device, error detection interfaces, and pneumatic blow devices to ensure operator safety. The touchscreen control also enables real-time monitoring for safer production management.
Yes! The TNC-TD/FD series guarantees JIS 1-grade accuracy (Japanese Industrial Standard), ideal for applications requiring tight tolerances, such as automotive parts, electronics, and aerospace components. The rotary encoder and digital mold height indicator further enhance precision.
They are widely used in automotive manufacturing, appliance production, metal forming, and precision engineering. Their split closed double/four-point structure ensures stability for heavy-duty tasks like blanking, stretching, and repeated deep drawing.
Maintenance is minimal with no flywheels, belts, or clutches. The modular design and pneumatic speedy connectors simplify part replacement. Optional features like the quick die change (Q.D.C.) further reduce downtime.
We offer automatic feeding systems, robotic arms, pneumatic die cushions, and preset counters for enhanced automation. Custom setups like T-shaped table movement (front/rear/left/right) are also available for complex workflows.
The visual production interface allows real-time monitoring of parameters like stroke count and speed. It streamlines quality management, production planning, and error diagnostics, ensuring consistent output.
Our range spans 400–4000 tons (TNC400TD to TNC4000TD), with adjustable strokes up to 1000 mm and stepless speed regulation (2–50 SPM). Check the technical table for detailed specifications per model.
Absolutely! The low-noise design (<75 dB) and 70% energy savings align with eco-friendly manufacturing standards. The low consumables design and absence of lubricant-dependent parts further reduce environmental impact.
Specializing in precision servo presses and efficient pneumatic presses, we deliver advanced stamping solutions for global manufacturing excellence.
@ 2025 FT Servo Press. All right reserved.
Fill out the form below, and we will be in touch shortly.