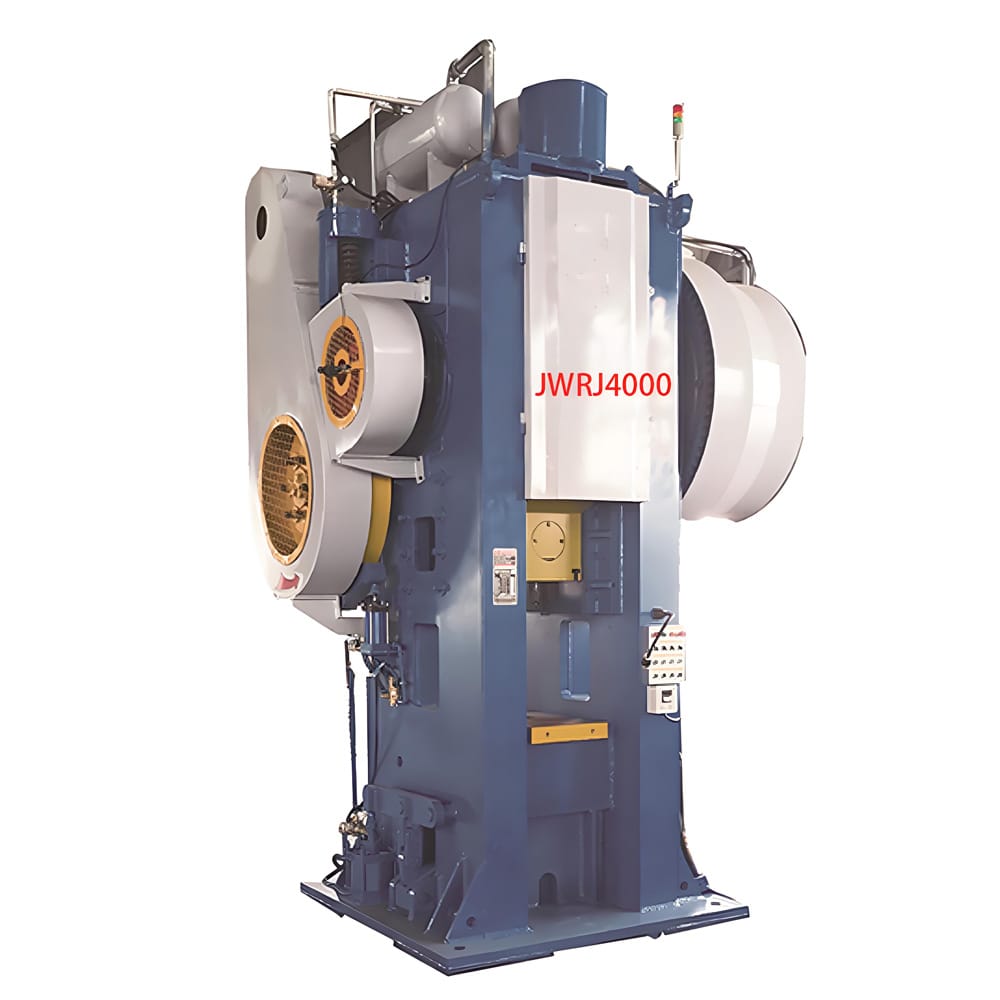
Customize Your TNB-EO Electric ServoPress: 80Tons | 110Tons | 160Tons | 200Tons | 250Tons | 300Tons | 400Tons | 600Tons | 800Tons
JIS Grade 1 certification, ideal for micro-stamping in electronics and medical industries.
Direct servo motor drive eliminates flywheel idling, saving over $20,000 annually (300 operating days).
High-rigidity closed-frame design reduces deformation (<0.02mm), supporting continuous 800-ton stamping.
Stepless speed control (2-120 SPM) and programmable stamping curves (6 modes: blanking, stretching, dwell, etc.).
Capable of handling diverse materials, from thin-gauge metals to high-strength alloys.
Precision gears, sensor housings (±0.02mm precision)
Lithium battery covers, deep-drawn aluminum shells (with die cushion)
Connector pins, shielding cases (high-speed 120 SPM)
Complex kitchenware shapes (low noise <65dB)
Model | TNB80EO | TNB110EO | TNB160EO | TNB200EO | TNB250EO | TNB300EO | TNB400EO | TNB600EO | TNB800EO |
---|---|---|---|---|---|---|---|---|---|
Nominal Force (kN) |
800 |
1100 |
1600 |
2000 |
2500 |
3000 |
4000 |
6000 |
8000 |
Slide Stroke (mm) |
150 |
180 |
200 |
200 |
250 |
250 |
250 |
250 |
250 |
Continuous Stroke |
2-120 |
2-70 |
2-70 |
2-65 |
2-60 |
2-50 |
2-40 |
2-40 |
2-40 |
Single Strokes Per Minute (SPM) |
unlimited |
unlimited |
unlimited |
unlimited |
unlimited |
unlimited |
unlimited |
unlimited |
unlimited |
Inching Strokes |
any |
any |
any |
any |
any |
any |
any |
any |
any |
Maximum Die Height (mm) |
340 |
360 |
400 |
420 |
460 |
500 |
600 |
700 |
700 |
Die Height Adjustment (mm) |
80 |
80 |
100 |
100 |
110 |
120 |
120 |
120 |
120 |
Upper Table Size (mm) |
650*420 |
800*470 |
840*560 |
860*600 |
960*650 |
1050*700 |
1050*800 |
1400*1000 |
1400*1100 |
Lower Table Size (mm) |
850*550 |
900*650 |
1000*700 |
1000*750 |
1200*770 |
1300*800 |
1350*900 |
1600*1100 |
1600*1200 |
Column distance(mm) |
870 |
920 |
1020 |
1020 |
1220 |
1340 |
1400 |
700*600 |
700*600 |
Shank Hole (mm) |
Φ50 |
Φ50 |
Φ65 |
Φ65 |
Φ65 |
Φ65 |
Φ65 |
Φ65 |
Φ65 |
Slide Adjustment Method |
Electric Adjustment |
Electric Adjustment |
Electric Adjustment |
Electric Adjustment |
Electric Adjustment |
Electric Adjustment |
Electric Adjustment |
Electric Adjustment |
Electric Adjustment |
Structural style(ton) |
link-type |
link-type |
link-type |
link-type |
link-type |
link-type |
link-type |
link-type |
link-type |
Guideway type |
Six-sided guideway |
Six-sided guideway |
Six-sided guideway |
Six-sided guideway |
Six-sided guideway |
Six-sided guideway |
Six-sided guideway |
Six-sided guideway |
Six-sided guideway |
Air Pressure (MPa) |
0.6 |
0.6 |
0.6 |
0.6 |
0.6 |
0.6 |
0.6 |
0.6 |
0.6 |
Press Accuracy |
JIS Class 1 |
JIS Class 1 |
JIS Class 1 |
JIS Class 1 |
JIS Class 1 |
JIS Class 1 |
JIS Class 1 |
JIS Class 1 |
JIS Class 1 |
FAQS For the Servo Press Industry
The TNB-EO servo press offers superior energy efficiency, precise control of the stamping curve via servo motor drive, and reduced noise levels compared to conventional presses. Its programmable stroke and speed adjustments ensure flexibility for complex precision stamping tasks while minimizing energy consumption.
The high rigidity O-frame minimizes deformation during operation, ensuring stability and extending the machine’s service life. This design also reduces vibration, critical for maintaining JIS 1 grade accuracy in high-precision applications.
Safety is prioritized with photoelectric safety devices, ergonomic controls, and man-machine protection designs. These features comply with global safety standards, protecting operators and ensuring compliance with industrial regulations.
Yes! The thoughtful electrical circuit design supports seamless integration with automatic feeding devices, robotic arms, and other automation equipment. Optional add-ons like quick die change (Q.D.C.) further streamline production workflows.
The servo motor drive reduces energy consumption by up to 30% compared to traditional presses. Its low energy consumption and stepless speed regulation optimize power usage during both idle and operational phases.
JIS 1 grade accuracy ensures consistent part quality, minimal material waste, and compliance with stringent manufacturing standards. This is vital for industries like automotive and electronics requiring micron-level precision.
Enhance your setup with pneumatic die cushion devices, knockout systems, or automatic feeding devices. The quick die change (Q.D.C.) option also minimizes downtime for high-mix production.
Absolutely! The electric mold height adjustment device and digital mold height indicator allow quick, precise adjustments, reducing setup time and improving operational efficiency.
Standard configurations include maintenance tools and a practical electric lubrication system to ensure smooth operation. We also offer comprehensive technical support and spare parts services.
The electric lubrication system automatically distributes oil to critical components, reducing wear and tear. This ensures long-term reliability and minimizes unplanned maintenance.
Specializing in precision servo presses and efficient pneumatic presses, we deliver advanced stamping solutions for global manufacturing excellence.
@ 2025 FT Servo Press. All right reserved.
Fill out the form below, and we will be in touch shortly.